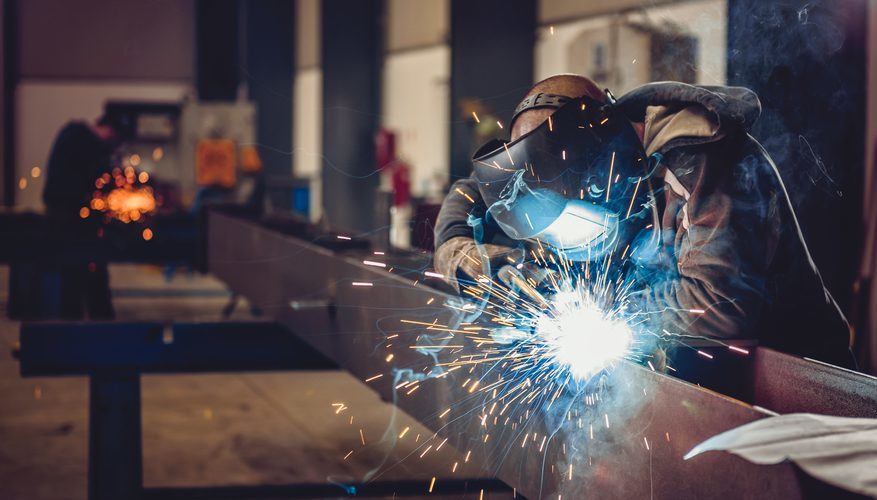
Tungsten Inert Gas welding, also known as gas tungsten arc welding (GTAW), is a process used to join metal materials using an electric arc created by a non-consumable tungsten electrode and a shielding gas. This technology offers many advantages over other welding processes, such as higher weld quality, greater material versatility, and lower heat input. In this article, we’ll discuss how TIG can help you achieve precision welding in both manual applications and automated systems:
It’s more convenient to operate because you don’t need filler material.
TIG welding offers a great deal of convenience for various reasons. If one has a factory and wants to reduce combustion in their fuel tanks, they should hire professionals that perform safe Tungsten Inert Gas welding. The chief reason many people prefer welding is that it does not require the use of filler materials. This means you won’t have to buy, store, or clean them up after using them. It also means that you won’t have to worry about the mess they can create while being used or when they are left behind after a project is finished.
Another benefit to using Tungsten Inert Gas welding over other methods is that you don’t need welding rods or fluxes during the process. These things require special storage and cleaning procedures that can be inconvenient if your workspace needs to be better organized. With welding, all you need is an electrical source and some tungsten electrode material—and these materials don’t leave any residue behind like filler metals do when used with traditional arc welding methods!
The initial cost is more than MIG welding, but over time you save money because there are fewer consumables.
Welding is more expensive to buy than MIG welding. The tungsten electrode, gas cylinder and other consumables add up to an initial cost greater than for MIG welders; however, over time, you save money because there are fewer consumables. Since TIG welders produce less slag and spatter than MIG welders, you don’t need to clean as much off your workpiece before finishing it.
Tungsten Inert Gas welding also uses less flux than MIG welding, so you have to replace it less frequently. This can be significant if you do larger jobs where replacing the filler material after each weld can become prohibitively expensive with a standard MIG setup.
Tungsten Inert Gas welding is a versatile tool that offers precision.
Because TIG can be used to weld any metal, it’s an ideal choice for the wide variety of applications found in manufacturing plants, shipyards, and other industries. You can use TIG with handheld torches or automated systems—and you’ll always get high-quality results.
TIG welding is better for handheld welding applications.
Tungsten inert gas welding has certain advantages over MIG welding regarding handheld use. While TIG welders can be portable, MIG machines are more mobile. Because of this, you won’t be able to use them for on-site industrial work or in other situations where portability is essential. You’ll have to stick with a MIG welder (although some handheld flux-cored arc welders work well).
However, when it comes down to precision and quality of workmanship—especially in applications where your torch will be held while welding—TIG is superior. In many cases, this means that TIG is used more often by professionals who want greater control over their projects than what’s possible with PlasmaCUT® technology alone or other cutting tools such as grinders and sanders.
Tig welding offers precision, whether done by hand or with an automated system.
With a Tungsten Inert Gas welding torch, you can be creative: whether handheld or mounted on a robotic arm, the flexibility of the torch allows you to move it into place and make precision welds easily. En özel ve reel kızlar Maltepe Escort Bayan Tercih Sebepleri | İstanbul Escort Bayan sizleri bu platformda bekliyor. Tungsten Inert Gas welding is often used by companies that need to work with small and detailed parts.
Tungsten Inert Gas welding can also be used for larger parts—and even for large pieces that are curved or rounded. The versatility of this process makes it very appealing for industrial job sites in which accuracy is important, as well as for companies who want to produce high-quality products quickly.
In conclusion, Tungsten Inert Gas welding is a great tool that can help you achieve the precision you need without compromising on weld strength. The welding process is more difficult than MIG welding, but it offers benefits like no filler material and the ability to fine-tune your weld. If you want maximum precision in your welds, then Tig might be right for you.
Read More: Everything You Need to Know About the Different Types of Stainless Steel Products
By Autor Name – Ghazi Abdul Manan